MAINTAINING TO PERFECTION
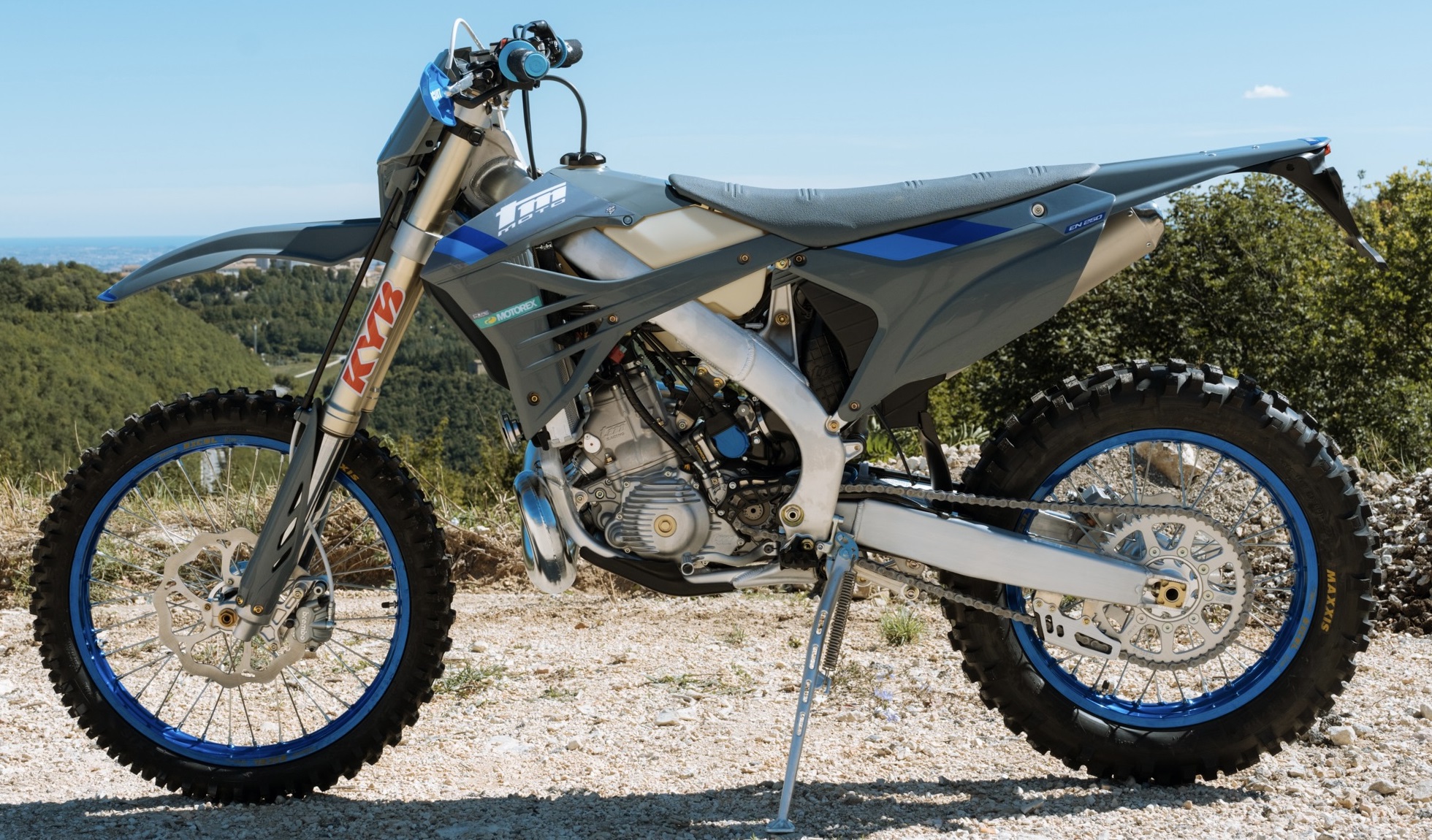
Washing Your TM Moto Machine:
For the best cleaning results it is advised that the ‘strip wash’ method is applied.
In preparation for washing the following steps are advised:
- Remove the seat, side panels and fuel tank and place to one side (on 2015 onward 4-Stroke models the fuel tank cannot be removed) ensuring that no particles of dirt can enter the fuel tap or EFi high pressure connector on the fuel tank, please note that on EFi equipped machines the high pressure fuel line connector must be uncoupled – there are several couplings that have been used over the model range years.
- 1: Early model coupling with black plastic fitting with ‘orange’ release fitting – push the connector towards the union on the tank whilst simultaneously pulling the orange snap connector release back towards the fuel line.
- 2: Later Fi 2T and some 4T models – push the connector towards the union on the tank whilst simultaneously pushing in the two white release clips, the connector will then pop off the tank union.
- 3: Later 4t Fi Models – hold the connector on the throttle body union and push in the two metal release clips, the connector will then ‘pop’ off the union.
- Note: you will also have to unplug the two-pin connector that supplies power to the fuel unit inside of the fuel tank on many models to completely remove the tank from the chassis / sub frame on later 4t models. Seal the exposed connector and union with a rubber glove ‘finger’ secured with a rubber band/zip-tie.
- Refitting: all types simply push the connector on until the locking mechanism of the snap release re-engages.
- On carbureted machines simply turn the fuel tap to the ‘OFF’ position, remove the sprung locking clip and pull the fuel line from the fuel tap on the tank. Ensure that both the fuel lines to either the carburetor or Efi system are ‘sealed’ to ensure no water can penetrate them, this can be achieved best by using the ‘finger’ from a rubber glove being placed over the fuel lines and secured with a rubber band / zip-tie.
- Remove the air filter element and its securing cage and place a clean cotton cloth into air intake boot of the machine, this will help to capture any excess moisture/debris that may enter the air boot whilst completing this process, clean around the ‘lip’ of the filter mounting plate to remove any excess dirt or filter oil and then secure the air intake boot by fitting a protective wash cover (‘filter covers’ – these are available from all good bike shops) and secure tightly using the centre screw. The fitment of an exhaust bung will also limit the chance of water entering the exhaust system and saturating the silencer packing which will lead to power loss and increased noise, again an exhaust bung can be purchased from all good bike shops. On machines that are excessively soiled it may be advisable to remove the front number plate, fork guards and also the radiator panels from the fuel tank to aid the cleaning process, these components can be hand washed after the machine chassis has been completed.
NOTE: For electric starter equipped 4-stroke machines it is advised to remove the battery before washing, the battery is contained in the battery tray beneath the seat and is simple to remove and replace. To remove the battery release the retaining strap, adjust the battery position to gain access to the terminal posts, being extremely careful not to create a short circuit remove the cables to the ‘negative’ terminal post first followed by the ‘positive’, please note the position of the cables and to which post they were attached, remove the battery from the machine and place out of the way until required later during preparation. The re-installation procedure is the reversal of removal procedure.
- The final step before actually washing the machine is a visual check to ensure that there are no areas exposed that could be susceptible to water ingress, components such as expansion pipes on larger capacity 2-stroke engine machines where the ‘front pipe’ mates to the cylinder and seal with 2 O-rings, is this a snug fit? , are the O-rings perished?, are there visible signs of black oil exiting through this connection?…is ‘YES’ then remove the pipe, replace the O-rings with new ones and using a small amount of sealant re-fit the pipe and allow it to cure before washing commences. Is the rubber sleeve joining the ‘front pipe’ to the silence in place or has it moved creating a possible place for water to enter the exhaust?, if ‘YES’ then re-fit the rubber sleeve correctly or replace with a new one if damaged before washing commences. It may also be advisable to block any engine breather pipes or venting hoses to reduce the risk of water ingress.
- Once you are happy that all of the above has been checked and verified to be correct you may proceed with washing your machine.
WARNING: Never Point a pressure washer or hose pipe directly at any bearings points, the carburetor or EFi components, the electrical components, the vent pipes, into the radiator cooling vanes or in the direction of any joints between components. Always work across the faces of components containing any bearings or ‘sensitive’ components, such as the linkage, steering stem, wheels hubs and ensure vent pipes are not in the direct line of any water jets, in some cases it may be advisable to block any vent pipes prior to washing.
- Never wash the bike in Freezing conditions, the water may freeze instantly on the machine and if it has penetrated any sensitive areas, such as throttle cables, it could lead to serious damage to the machine upon starting the engine and injury to the operator if used immediately after washing.
- Always adhere to the following procedures and checks and never run the bike without completing them first, failure to do so may lead to machine damage and possible injury.
Washing: Using either a pressure washer or a hose pipe give the bike a covering of water to allow it to ‘soak’ into any stubborn areas, leave this for a few minutes to allow penetration of the water into the dirt particles. Once any hardened dirt has had chance to ‘soften’ then proceed to remove the bulk of the dirt with the pressure washer or hose pipe from the machine, paying attention to the heavily soiled areas first such as underneath the mudguards, the wheels, the swinging arm, brake caliper components and around the final drive area from the engine, the chain, chain guides and rear sprocket, removing the larger areas of dirt first will aid rotation of the wheels. The brake calipers can be ‘compressed’ by hand allowing the brake pads to release any contact with the braking disc surfaces, this will allow easier rotation of the wheels. It may also be advised that the machine be laid on its side to gain better access to the bottom of the machine and the harder to reach areas such as the sump of the engine, the suspension linkage and the bottom of the forks legs for example, please pay attention not direct any jets of water at the breather pipes of the engine or carburetor.
NOTE: If you separate the brake pads contact with the brake disc to aid rotation you must ensure the brakes are ‘pumped’ using the control levers sufficiently after washing to ensure the brake pads are back in contact with the brake discs surface, failure to adhere to this could lead to an accident.
Any hard to remove ingrained dirt or ‘stubborn’ areas can be treated with a cleaning brush as opposed to being continuously ‘blasted’ with water to avoid prolonged saturation to expensive components and possible water ingress. Once the heavy material has been removed give the bike a liberal wash to remove the residual dirt in preparation for spraying the bike with a recognised brand of salt-free, non-corrosive bike detergent – ‘Moto-Verde’ for example, which is used and recommended by TM UK.
NOTE: TM strictly prohibits the use of Traffic Film Remover (TFR) products in any dilution. These types of cleaner can lead to irreparable damage to plastic components and decals, damage to billet aluminium by eroding its top layer leaving a dull, laclustre finish, and the breakdown of any greases in bearings on the machine leading to shortened service life and/or failure.
After the application of the bike cleaner has taken place following the products instructions and guidelines rinse the machine off, any stubborn areas can again be hand brushed and aluminium frames and sub-frames can be brightened and cleaned using a fine ‘Scotch-brite’ pad used in the direction of the material grain to give a better finish, this can also be a useful tip for cleaning the expansion/exhaust pipes and return them to their natural finish.
The inside of the ‘airbox’ on the machine should also be cleaned thoroughly, liberal application of bike cleaner onto the damp airbox followed by manual brushing or wiping with cloth should ensure that all dirt particles and any filter oil residue are removed, one thoroughly clean rinse liberally to remove all dirt and cleaning product. Any areas that are still not to satisfaction can be re-cleaned, again spraying bike cleaner onto the damp surfaces allow the required penetration time or manually brush or wipe the surfaces to remove and dirt, always pay attention to areas such as, the radiators – working form the rear to the front to ‘blow out’ and dirt forced into the front of them whilst riding (the radiator guards can removed to aid cleaning) the suspension linkage and its components, brake calipers, the engine surfaces, sprockets and chains (chains can be ‘wire brushed’ if particularly dirty or corroded), around the carburetor/Efi components (hand washing/brushing/wiping is advised here), around the front fork stanchions, fork leg bottoms and behind the fork guards, around any controls such as the brake and clutch cylinders and throttle assembly (again hand washing/brushing/wiping is advised), the cleaning of any dirt from electrical connection is also advised to ensure good conductivity and to reduce electrical breakdowns from corrosion. Once the machine, its components and any areas that require hand washing and inspection are treated a final rinse is required.
Once the final rinse has taken place a visual check of the entire machine should be completed to ensure that there are no areas left dirty such as the bottom of the chassis and engine, if there are any areas you believe not to be clean repeat the cleaning process for those areas.
Now the main chassis of the bike is clean you can clean the parts removed earlier, the tank, seat and side panels (in some cases it useful to give the side panels a quick wash prior to removing from the machine especially if they are heavily soiled), cleaning the tank and seat is best done by hand as opposed to using a low pressure washer, the pressurised water jet could force water into the fuel cap venting system or into the seat foam causing unnecessary problems later on.
Upon completion of washing and rinsing your TM Moto machine it is advantageous to have some form of compressed air supply to allow you to ‘blow’ any excess water from the machine, paying attention to the radiators, engine and fuel system components, airbox, calipers, front fork stanchions and around all of the machine control levers and throttle, on 4-Stroke machines it is also advisable to remove the spark plug cap and clean and dry the recess in the cylinder head that the spark plug resides in, paying attention on the EFi machines to ensure that the ‘drain gallery’, which allows excess water to escape from the spark plug recess, is free from obstruction and that all moisture is removed. If a compressed air supply is unavailable then some cloth will suffice to wipe dry the areas and remove most of the residual moisture.
After removing most of the water and moisture it is advisable to spray the machine (avoiding the calipers, the brake pads and brake discs) with a liberal coating of water repellent and protector, a good example of this type of product is Moto Verde ‘Afterwash’, this ensures any residual moisture is repelled and that the bike and it’s components are coated with a light protective film which inhibits oxidization forming on the machines components. The chain should be treated with a good quality chain lubricant and excess should be wiped off once it has penetrated into the chain links.
Prior to running the machine after the cleaning procedure the following steps must be completed:
Remove all of the protective components used during the washing procedure, exhaust bung, filter cover and cloth, fuel line covers, etc.
- Wipe the inside of the airbox and airboot with a clean cloth to remove and particles that may have entered the intake system.
- Drain the carburetor by removing the drain bung on the bottom of the float bowl, on two stroke machines it will be necessary to loosen the two jubilee clips securing the carburetor in-place to allow you to rotate it for better access to the drain bung.
- Use a cloth to soak up the draining fuel and if you have a compressed air supply gently blow any excess fuel/moisture from the float bowl, it may be advisable on 2-Stroke machines to remove the pilot and main jet using a small flat blade screwdriver and a 6mm hexagonal socket to ensure there are no blockages in either jet.
- Replace any removed jet carefully and do not over-tighten, replace the drain bung and secure the carburettor retaining clips you have loosened.
- On 2-Stroke engine machines it is advisable after the cleaning process to remove the ignition cover and expel any moisture using compressed air or a cloth, once the moisture has been removed spray with a water repellent and protector to ensure the formation of oxidization cannot occur. Moisture can form in this area due ‘sweating’ and prolonged exposure to any moisture could lead to corrosion of the electrical components causing bad running or complete failure.
- On all machines pay particular attention to remove any residual moisture from all of the electrical components and any joints or connections between the electrical circuit parts, any build up moisture could lead to bad running and or component corrosion and failure.
NOTE: It is recommended for all machines that the connector between the CDi/ECU and the main wiring loom is never disconnected, the connection pins contained within these units are numerous and are constructed very finely, any error in removing or re-fitting the connector could potentially lead to breakages of the pins. These complex electrical units are not serviceable items due to the ‘potting’ compound they are sealed in during production to protect them from the vigours of day-to-day off road riding, moisture and vibration, any breakages to the connection pins could cause poor engine performance and engine component damage and render the CDi/ECU unit useless. Replace the air filter element with a clean re-oiled filter and secure to the filter mounting plate using the centre screw paying attention to the mounting lug and that it is seated in its relevant locating hole on the mounting plate.
- Check coolant level and top up if necessary with a good quality aluminium safe coolant/antifreeze.Replace the fuel tank, side panels and seat, and any other plastic parts you have removed during the cleaning process.
NOTE: It is advisable that any panel fixings or fasteners be treated with a light coating of grease prior to refitting, paying particular attention to not over-tighten the bolts that fix the radiator panels to the fuel tank. The fixing points in the fuel tank are constructed from brass whereas the fixing bolts are steel, these two metals can react and increase there bond together, if the bolts are over-tightened there is a chance that they may not be removed and may in fact damage the brass fixing points in the fuel tank. Remember that on EFi equipped machine to refit the power connector back into the fuel tank pump system and on all machines ensure that the throttle cables are not trapped between the fuel tank and the chassis or any other components binding the cables tightly and not allowing free movement of the throttle.
- Give the machine a thorough visual check-over one it has been re-assembled, it is advisable to check all fixings and fastenings on the machine, the spokes, chain tension, sprocket bolts, engine mounting bolts, sub-frame mounting bolts, triple clamp bolts and steering stem nut, caliper fixing bolts, brake pad thicknesses and tyre condition and pressures, ensure all of the controls are operating as necessary and that the throttle is free to open and close at all steering angles.
You may then start your machine as per normal, run the engine up to operating temperature, visually check the machine over again, listen for any irregularities and check controls once more before riding.